Using Topstar water chillers to reduce corrosion risk in North American injection molding
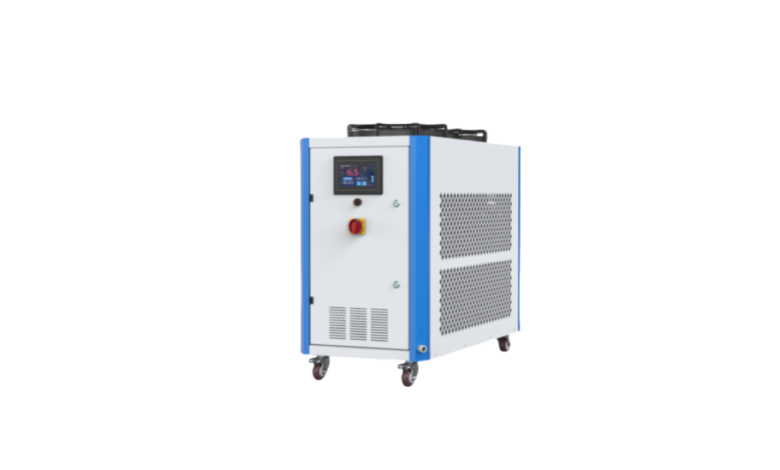
Corrosion in injection molding systems is a costly and ongoing problem, especially in North America, exacerbated by variable water quality and environmental conditions. Water chillers are critical in regulating mold temperatures, but poor-quality cooling water can lead to rust, scaling, and equipment failure. For example, a 2023 study by the Plastics Industry Association found that 40% of North American manufacturers experienced downtime due to corrosion-related issues, costing an average of tens of thousands of dollars per incident.
Topstar’s water chillers address this challenge by incorporating advanced filtration and corrosion-resistant materials. With Topstar’s chillers, corrosion-related downtime has been reduced by 60%. By preventing rust and scaling, these systems extend equipment life and ensure consistent product quality.
Chillers: How Topstar’s Anti-Corrosion Technology Works
Topstar’s water chillers feature cutting-edge anti-corrosion technology, including stainless steel heat exchangers and titanium-coated tubes. These materials resist oxidation and chemical degradation even in harsh environments. For example, a Texas-based electronics manufacturer reported zero corrosion issues after 18 months of using Topstar chillers despite the high mineral content in the region’s water. In addition, Topstar’s water chiller uses a closed-loop cooling system that prevents contaminants from entering the water supply. This is particularly beneficial in hard-water areas, where minerals such as calcium and magnesium can cause scale buildup. A Canadian packaging company reduced maintenance costs by 30% after adopting Topstar’s chillers, highlighting their effectiveness in preventing corrosion.
See also: Benefits of AI Face Swap Technology in Content Creation
Ensuring Consistent Mold Temperature Control with Water Chillers
Corrosion isn’t just a maintenance issue – it can also disrupt mold temperature control, causing defects such as warping or sink marks. Topstar’s water chillers maintain precise temperature control (±0.5°C), ensuring uniform cooling and reducing the risk of mold thermal stress. The chiller’s adaptive cooling algorithm also adjusts water flow based on real-time data to prevent overheating or undercooling. A case study from a toy manufacturer in Ohio showed a 25% reduction in cycle time because the chiller optimized cooling for each mold. Topstar’s chillers improve product quality and production efficiency by ensuring consistent temperatures.
Reduce Energy Costs While Preventing Corrosion
Corrosion often causes inefficiencies, such as clogged pipes or reduced heat transfer, which increase energy costs. To address this problem, Topstar’s chillers are designed with energy-saving features, including variable-speed pumps and heat recovery systems. A New York-based packaging plant reduced energy consumption by 20% after upgrading to Topstar’s chillers, saving tens of thousands of dollars annually.
The water chiller’s intelligent energy management system also monitors water quality and flow rates, alerting operators before potential problems escalate. A case study of a consumer goods manufacturer in Florida showed a 50% reduction in energy-related maintenance costs because the chiller’s predictive analytics prevented inefficiencies caused by corrosion. Combining energy savings with corrosion prevention, Topstar’s chillers offer a dual benefit to cost-conscious manufacturers.
Compatibility with North American water conditions
The variety of water conditions in North America—from hard water in the Midwest to salt water in coastal areas—presents unique challenges for injection molding. Topstar’s chillers are designed to handle these changes with customizable filtration systems and corrosion-resistant coatings. Chillers also support water treatment additives, such as inhibitors and biocides, which further reduce the risk of corrosion. A case study from a Chicago-based automotive supplier showed a 40% improvement in water quality after integrating Topstar’s water chillers with a customized treatment system. Topstar’s water chillers ensure reliable performance throughout North America by adapting to local conditions.
Improving Sustainability Through Corrosion Prevention
Corrosion damages equipment and creates environmental waste, as corroded parts often need to be replaced. Topstar’s chillers promote sustainability by extending equipment life and reducing material waste. The chillers’ energy-efficient design aligns with sustainability goals, such as reducing greenhouse gas emissions. A case study from a California-based technology company showed a 30% reduction in energy-related emissions after upgrading to Topstar’s water chillers. By combining corrosion prevention with environmentally friendly features, these systems help manufacturers achieve operational and environmental goals.
Ultimately
Topstar’s water chillers have transformed the North American injection molding industry with