Foam Moulding: An Innovative Approach to Polyurethane Foam
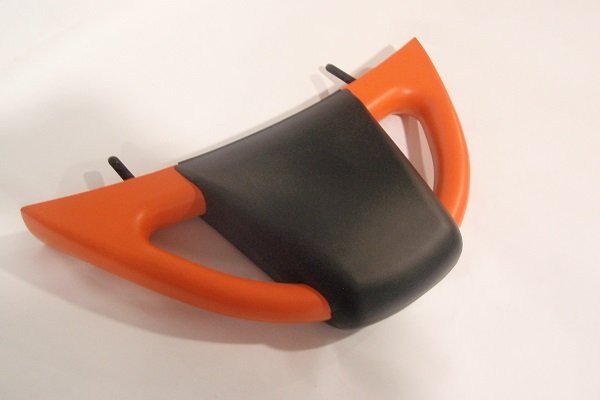
Introduction to Foam Moulding
Foam moulding is an advanced manufacturing process used to create high-quality, durable, and flexible polyurethane foam products. This technique is widely employed in various industries due to its versatility, strength, and cost-effectiveness. The process involves the use of moulds to shape polyurethane foam into specific forms, making it suitable for applications such as furniture components, vehicle interiors, industrial equipment, and more.
Polyurethane foam is a highly adaptable material known for its ability to provide superior cushioning, impact resistance, and thermal insulation. Foam moulding techniques, such as integral skin moulding and rigid foam moulding, enable manufacturers to produce products with varying levels of density and hardness while maintaining a protective outer skin.
The Foam Moulding Process
The production of polyurethane foam mouldings involves a chemical reaction between two main components that are mixed and poured into a mould. The key steps in the foam moulding process include:
- Material Preparation: The polyurethane components are carefully measured and combined to ensure a consistent reaction and final product quality.
- Mould Filling: The mixture is poured into a mould that defines the final shape and texture of the product.
- Curing: The chemical reaction causes the material to expand and harden within the mould, forming a strong and durable foam structure.
- Trimming and Finishing: Once the foam has fully cured, excess material is trimmed, and additional coatings may be applied for enhanced durability and aesthetic appeal.
Types of Polyurethane Foam Moulding
1. Integral Skin Foam Moulding
Integral skin foam moulding, also known as self-skin moulding, produces foam products with a tough, tear-resistant outer skin and a softer, cushioned core. This type of polyurethane foam is ideal for applications requiring durability and comfort, such as grab handles, armrests, steering wheels, and seating components.
2. Rigid and Flexible Foam Moulding
Rigid polyurethane foam is widely used for insulation, structural reinforcements, and impact-resistant components. On the other hand, flexible foam moulding is preferred for products that require softness and adaptability, such as padding and cushions.
3. Impact Foam Moulding
Impact foam moulding involves creating highly durable polyurethane products that can withstand mechanical stress and external pressure. This makes it suitable for safety products, sports equipment, and industrial applications.
4. RIM (Reaction Injection Moulding)
RIM moulding is a specialized foam moulding process that produces lightweight yet strong polyurethane components. It is commonly used in automotive and marine applications due to its excellent mechanical properties.
Applications of Polyurethane Foam Moulding
Polyurethane foam moulding is utilized in various industries, including:
- Automotive: Gear stick knobs, headrests, armrests, and seating components.
- Marine: Protective padding and seating for boats and yachts.
- Furniture: High-quality cushions, decorative trims, and ergonomic components.
- Industrial Equipment: Safety padding, insulation panels, and noise reduction barriers.
- Sports and Leisure: Protective gear, exercise equipment padding, and impact-resistant components.
Benefits of Polyurethane Foam Moulding
Foam moulding offers several advantages over traditional manufacturing methods, making it a preferred choice for many industries. Some of the key benefits include:
1. Durability and Strength
Polyurethane foam mouldings are known for their resilience, impact resistance, and ability to withstand harsh environmental conditions. The integral skin provides added protection against wear and tear, making it suitable for high-usage applications.
2. Customizable Designs
Manufacturers can create bespoke designs with specific textures, colors, and hardness levels to meet customer requirements. The mould tooling can be chemically etched to give the surface a leather-like texture or other aesthetic finishes.
3. Lightweight and Flexible
Despite their durability, polyurethane foam products remain lightweight, making them easy to handle and install. The flexibility of foam allows it to conform to various shapes and contours.
4. Thermal and Sound Insulation
Polyurethane foam provides excellent thermal insulation, reducing heat loss and improving energy efficiency. Additionally, acoustic barrier products made from polyurethane foam help in noise reduction by absorbing sound waves.
5. Resistance to Environmental Factors
Foam moulded products can be coated with UV-stable paint, ensuring resistance to sunlight exposure and color fading. They also offer excellent resistance to moisture and fire when treated with fire-retardant compounds.
Future of Polyurethane Foam Moulding
With advancements in material science and moulding technology, polyurethane foam moulding continues to evolve. The industry is seeing increased adoption of eco-friendly materials and sustainable production methods to reduce environmental impact. Additionally, innovations in CAD design and 3D printing are enhancing the precision and efficiency of foam moulding processes.
Read also: Get the Best from Your Smart Home Control System
Conclusion
Foam moulding is a highly effective manufacturing technique that produces durable, flexible, and customizable polyurethane foam products. Its applications span across multiple industries, providing essential components for automotive, marine, furniture, and industrial sectors. With its numerous benefits, including durability, lightweight properties, and insulation capabilities, polyurethane foam moulding remains a crucial technology for modern product development. As new advancements emerge, the future of foam moulding looks promising, offering even more innovative solutions for various applications.